Key Takeaways
- CNC machining rims offer unmatched precision, enabling intricate designs, tight tolerances, and consistent quality for high-performance automotive applications.
- This process supports extensive customization, allowing for unique spoke patterns, bolt configurations, and surface finishes tailored to individual preferences or branding.
- Rims produced through CNC machining exhibit superior strength, lightweight construction, and excellent durability, making them ideal for racing, commercial, and luxury vehicles.
- Popular materials include 6061-T6 aluminum due to its strength, weight advantages, and corrosion resistance, while steel and specialty metals are used in niche applications.
- Selecting CNC machined rims requires balancing mechanical performance, visual appeal, and budget considerations to meet specific requirements.
- Routine cleaning, careful inspection, and protective coatings are essential for maintaining the appearance and longevity of CNC machined rims.
CNC machining rims utilises computer-controlled technology to manufacture wheels with exceptional precision, achieving tolerances as tight as ±0.01mm. This advanced process enables extensive customisation including unique spoke patterns, bolt configurations, and surface finishes from materials like 6061-T6 aluminium. CNC Machining delivers superior strength, lightweight construction, and consistent quality for automotive, racing, and luxury vehicle applications where precision and performance are paramount.
What Are CNC Machining Rims?
CNC machining rims use computer numerical control technology to manufacture wheels from solid materials like forged aluminum or steel. Automated processes guide cutting tools based on programmed designs, producing rims with tolerances as tight as ±0.01 mm. Manufacturers select CNC machined rims when high levels of symmetry, balance, and surface finish matter for applications including automotive, aerospace, and motorsports sectors. These rims often display intricate patterns, optimized weight distribution, and uniform strength across all segments.
For example, companies create custom offsets, bolt patterns, and unique spoke configurations using five-axis CNC machines. Each run can match specific vehicle requirements or performance targets, such as lightweight racing needs or load-bearing demands for commercial fleets. CNC machining allows fast prototyping and repeatable quality, making it possible to deliver consistent product runs for aftermarket customizations or OEM production orders.
Key Benefits of CNC Machining Rims
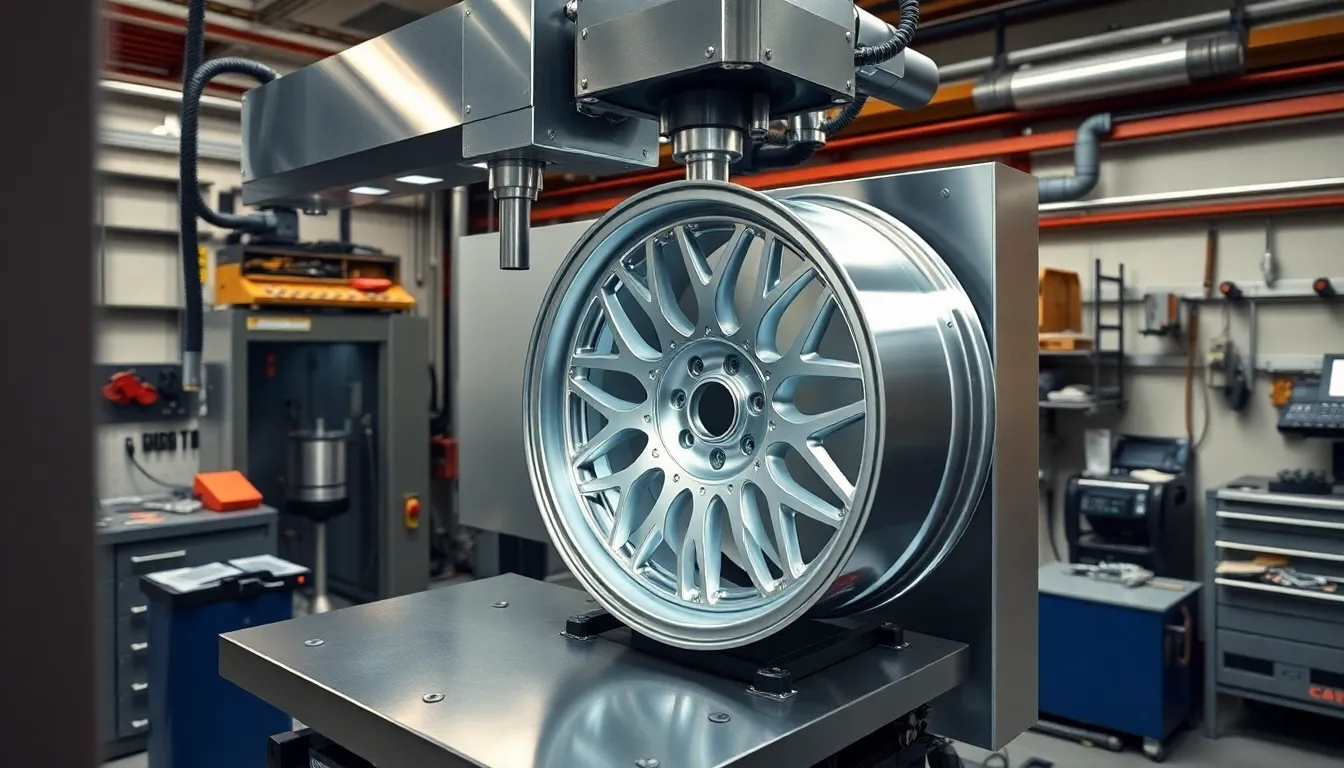
CNC machining rims provides advantages for precision manufacturing in the automotive and racing sectors. This process addresses critical demands for accuracy, flexible design, and mechanical performance in modern wheel production.
Enhanced Precision and Consistency
CNC machining achieves tight tolerances in rim production, with precision reaching up to 0.0025mm. This high accuracy ensures each rim meets exact specifications, resulting in uniform fit and function across production runs. Automated machine instructions minimize human error and replicate designs precisely. Automotive manufacturers and custom shops consistently produce symmetrical, balanced rims that meet performance and safety standards. This precision supports seamless mounting and optimal wheel alignment, which are essential for high-speed and high-load applications.
Customization Options
CNC machining facilitates intricate customization of rim features, enabling unique appearances and functional enhancements. Advanced CNC machines with 4-axis or 5-axis capability cut complex patterns, such as personalized spokes, custom offsets, and special bolt patterns. Shops offer creative surface finishes and textures, tailoring rims to owner preferences or branding. Limited-edition wheels or special runs use CNC’s flexibility for quick design changes and rapid prototyping. These options meet the demand for distinctive designs in custom, luxury, or motorsport applications.
Improved Strength and Durability
CNC machining controls material removal precisely, optimizing the structural integrity of rims. Consistent defect-free cutting processes maximize strength while allowing for reduced weight when desirable, directly contributing to performance and fuel efficiency. CNC-machined rims demonstrate high durability and resistance to fatigue, important for sport and high-performance vehicles. The process also supports easier repair and refurbishment, using specialized CNC lathes to restore surface finish and structure, extending the usable lifespan and value of each rim.
Comparison: CNC Machining vs. Traditional Rim Manufacturing
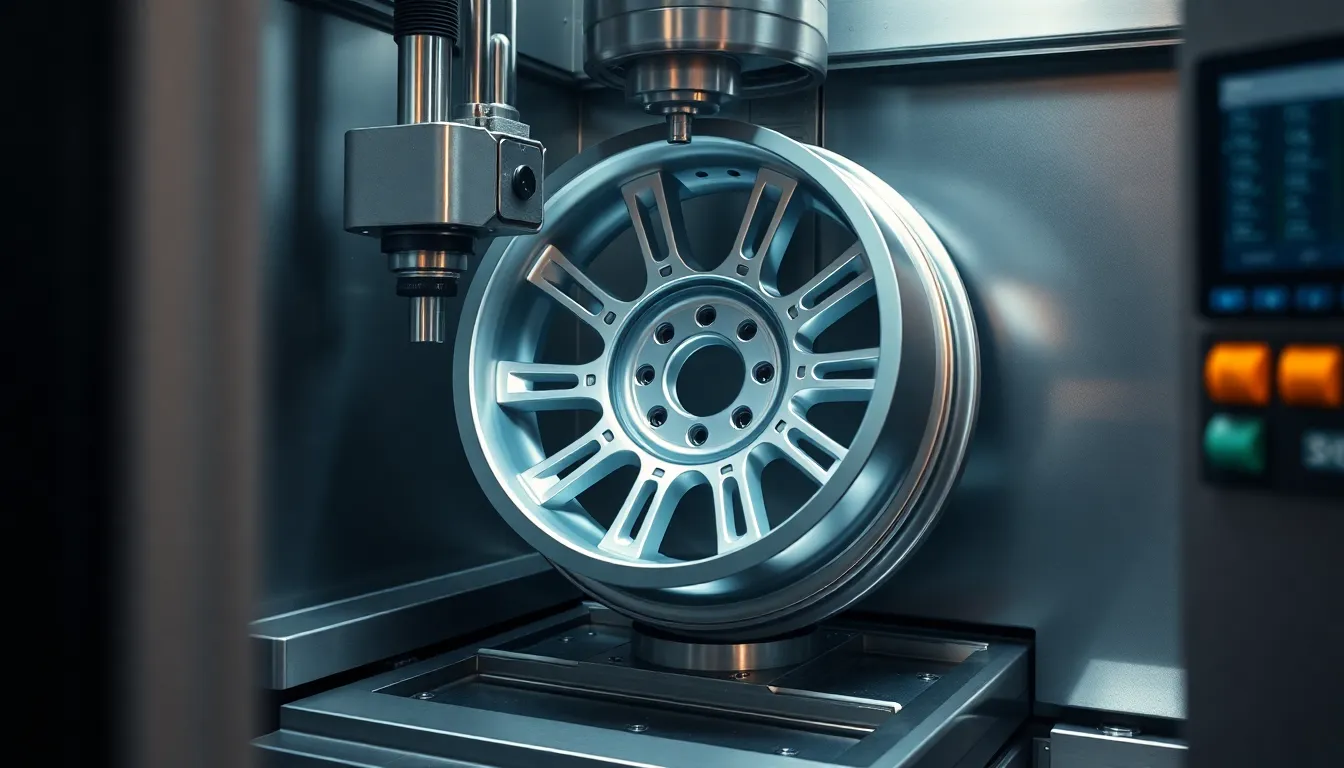
CNC machining rims achieve high precision and repeatability since automated systems follow programmed paths, maintaining tolerances as close as ±0.01 mm. Traditional rim manufacturing depends on manual tools and operator skill, causing tolerances to vary from rim to rim. CNC processes handle complex shapes and lightweight designs; multi-spoke, hollow-core, and intricate surfaces appear consistently in rims machined this way. Traditional methods restrict designs to simpler, heavier profiles because manual control limits geometry.
Manufacturers using CNC machining streamline production through automation: production lines run faster, labor needs drop, and material waste decreases. Traditional processing remains slower, with higher per-unit labor requirements. For large orders, CNC efficiency lowers total costs over time, while traditional methods might appear less expensive initially for a single rim or short run.
Manual manufacturing adapts quickly to low volume custom rims, allowing for frequent setup changes without programming. CNC machining offers superior consistency but less flexibility for small, one-off runs due to the setup overhead. Most high-volume, precision rim contracts use CNC technology, while some low-volume specialty requests still rely on traditional hand operations.
Feature | CNC Rim Manufacturing | Traditional Rim Manufacturing |
---|---|---|
Precision | High, ±0.01 mm | Operator-dependent |
Complexity | Intricate, lightweight | Simple, heavier |
Production Efficiency | Automated, fast | Manual, slower |
Labor/Skill | Programming, low manual | High manual |
Cost-Effectiveness | Lower long-term | Higher long-term |
Flexibility | Low for one-offs | High for custom |
Popular Materials Used for CNC Machining Rims
6061-T6 aluminum is the most widely used material for CNC machining rims due to its optimal blend of strength-to-weight ratio, machinability, and natural corrosion resistance. This forged aluminum alloy, when heat-treated to a T6 temper, provides a high yield strength required for lightweight and durable rims. Most automotive manufacturers rely on 6061-T6 for wheels used in performance vehicles, with typical machining tolerances of ±0.001 inch. Applications that require different strength or corrosion profiles sometimes use other aluminum alloys, but these remain less common.
Steel and stainless steel offer higher tensile strength and durability than aluminum, though their increased weight limits usage for rims to niche or specialty purposes. Manufacturers often use steel and stainless steel more for CNC tooling and support fixtures rather than the rims themselves. Brass, titanium, and copper may appear in specialized rim components or for visual accenting, but rarely serve as the primary rim material due to cost or mechanical limitations.
Most CNC-machined rims originate from forged aluminum billets, which enable tight quality control and allow dimensional tolerances critical for vehicle balance and safety. Surface finishes of about 63 RA (roughness average) are routinely achieved to satisfy both functional and cosmetic requirements. Rims produced from these materials commonly find application in high-performance automotive, motorsport, and premium aftermarket sectors.
Factors to Consider When Choosing CNC Machining Rims
Selecting CNC machining rims involves evaluating mechanical performance, appearance, and cost to meet the specific needs for each application.
Performance Requirements
Performance requirements for CNC machining rims depend on material strength, durability, and fit. Forged aluminum, such as 6061-T6, offers high mechanical strength and resistance to fatigue for demanding automotive and motorsport uses. Machining precision, with tolerances as tight as ±0.01 mm, ensures rims match specific bolt patterns, offsets, and hub sizes. Smaller wheels provide smoother driving, while larger rims improve handling and appearance. Accurate fit reduces stress on mounting points and improves driving safety. High-strength materials and exact cutting parameters maintain rim integrity after long exposure to road forces.
Aesthetic Preferences
Aesthetic preferences influence design, finish, and surface patterns possible with CNC machining. Machined and brushed finishes, often used for high-end or custom vehicles, create reflective surfaces with intricate spoke designs. CNC processes allow unique patterns like split-spoke, mesh, or multi-piece configurations—common in performance or luxury models. The finish and detail should match vehicle style, often requiring manual hand-finishing for a premium look, which may extend production time by 8 hours per wheel. Color choices, surface coatings, and etched details improve visual appeal and can support personal or branded themes.
Budget Considerations
Budget considerations for CNC machining rims include material choice, design complexity, wheel size, and type of finish. Custom configurations, such as unique bolt patterns or intricate designs, increase setup and machining time—raising costs. Premium finishes, like mirror-polished or hand-brushed surfaces, demand extra labor. Efficient material use and minimal waste lower production expenses. Initial production of CNC machined rims can start at mid-tier pricing, but exclusive options with multi-stage finishing and custom features can increase costs. Setting a clear budget before sourcing ensures options align with both technical and design needs.
Top Brands Offering CNC Machining Rims
Top rim manufacturers use CNC machining to deliver high-precision, durable wheels for automotive performance and style.
- Vossen Wheels: Vossen manufactures in the U.S. using aerospace-grade 6061-T6 aluminum. The company operates 22 advanced CNC machines, including vertical lathes and mills. Its proprietary eight-step machining process produces forged rims with superior finish, accuracy, and structural reliability. Vossen rims are popular for custom offsets, spoke designs, and luxury vehicle fitments.
- MAZAK: MAZAK produces CNC machines widely deployed in wheel manufacturing. Its multi-tasking machines, such as the INTEGREX i-500, handle complex automotive parts, including forged and billet rims. High spindle speeds and integrated milling functions deliver efficiency and tight tolerances. Many OEMs and large-volume rim producers use MAZAK technology.
- CHIRON: CHIRON specializes in high-speed vertical machining centers. German-made CHIRON equipment features rapid tool changes and high rigidity, supporting fast throughput on complex wheel geometries. Several automotive wheel factories trust CHIRON for processing custom multi-spoke and high-strength rim designs.
- HAAS, DMG MORI, and Okuma: HAAS automation, DMG MORI, and Okuma supply CNC lathes and mills installed in rim production lines globally. These brands help meet demand for complex, lightweight wheel styles with minimal runout and repeatable precision.
Brand | CNC Strengths | Industry Focus |
---|---|---|
Vossen | In-house forged, high design depth | Custom/luxury wheels |
MAZAK | Multi-tasking, large volume | OEM/high-rate manufacturing |
CHIRON | High-speed, tool change efficiency | Complex/rapid prototyping |
HAAS/DMG MORI/Okuma | Versatile, global support | Standard/performance applications |
Maintenance and Care Tips for CNC Machined Rims
Consistent maintenance preserves the precision and appearance of CNC machined rims. Cleaning removes dirt, brake dust, and road grime—common examples include residue from pads and corrosive compounds from de-icing salts. Soft microfiber towels or rim-specific brushes prevent scratches, while abrasive pads or harsh chemicals create surface damage that leads to corrosion.
Routine inspection detects scratches, cracks, or bends. Damage most often results from pothole impacts and curb scrapes. Early identification stops small flaws from developing into major safety or balance issues.
Protective coatings like wax or sealants designed for aluminum or machined finishes form a barrier against oxidation, environmental contaminants, and water spots. These coatings maintain the original luster of diamond-cut or brushed surfaces.
Exposure to salt, road chemicals, and extreme weather accelerates staining and corrosion. Quick rinsing after such events minimizes risk, especially during winter months. Yijin Hardware recommends regular cleaning intervals for rims exposed to aggressive conditions in industrial or coastal locations.
Proper manufacturing equipment care also ensures rim quality. Technicians at Yijin Hardware maintain CNC machines by cleaning work areas, lubricating moving parts, inspecting tool sharpness, calibrating spindle alignment, and monitoring coolant and air systems. This discipline reduces rim defects and extends the service life of both rims and machinery.
About Yijin Hardware
Yijin Hardware, located in Homestead, FL, is a leading provider of precision manufacturing services, specialising in CNC machining, sheet metal fabrication, and custom fasteners.
Under the leadership of CEO Gavin Yi, Yijin Hardware also offers additional solutions such as die casting, injection molding, and 3D printing to support various industries, including automotive, aerospace, medical, and energy. With a commitment to high-quality manufacturing and precision engineering, Yijin Hardware delivers tailored solutions to meet the unique needs of its clients.
Contact:
Gavin Yi, CEO
Phone: +1 626 263 5841
Email: [email protected]
Website: www.yijinsolution.com
Location:
760 NW 10th Ave, Homestead, FL 33030
Frequently Asked Questions
What is CNC machining for rims?
CNC machining for rims is a manufacturing process that uses computer-controlled machines to cut, shape, and finish wheels from solid metal, such as forged aluminum or steel. This process ensures high precision, allowing for detailed designs, tight tolerances, and a perfect fit for various vehicles.
What are the main benefits of CNC machined rims?
CNC machined rims offer exceptional accuracy, consistency, and customization options. They feature superior symmetry, balance, and surface finish for better performance and aesthetics. The process also enables quick prototyping, easy repair, lightweight construction, and reduced material waste compared to traditional methods.
How do CNC machined rims compare to traditionally made rims?
CNC machined rims achieve tighter tolerances and more complex designs due to automated precision. Traditional methods rely on manual tools, leading to greater variation, simpler designs, and usually heavier rims. CNC machining is more suitable for high-volume, precise orders, while manual methods may be used for low-volume custom jobs.
What materials are commonly used in CNC machined rims?
Forged 6061-T6 aluminum is the most popular material for CNC machined rims, valued for its strength, low weight, and corrosion resistance. Some rims are also made from steel, stainless steel, or other metals, but these are generally heavier or used for specialized applications.
Can CNC machining rims be customized?
Yes, CNC machining allows for extensive customization, including personalized offsets, bolt patterns, and spoke designs. This makes it possible to tailor rims for specific vehicles, unique styles, or performance needs, especially in luxury or motorsports applications.
What should I consider when choosing CNC machined rims?
Consider your vehicle’s performance requirements, desired design, and budget. Material quality, fitment, style, and finish can all affect performance and cost. Setting a clear budget and understanding your performance and aesthetic needs will help you choose the right rims.
Which brands are known for high-quality CNC machined rims?
Top brands include Vossen Wheels, MAZAK, CHIRON, HAAS, DMG MORI, and Okuma. Vossen specializes in luxury forged rims, while MAZAK, CHIRON, and the others produce advanced CNC machinery that enables high-precision wheel manufacturing worldwide.
How should I care for CNC machined rims?
Clean your CNC machined rims regularly with a soft microfiber towel or specialized brush to remove debris and corrosive elements. Apply protective coatings to prevent oxidation and inspect them for damage after impacts. Proper care extends both the rim’s appearance and lifespan.